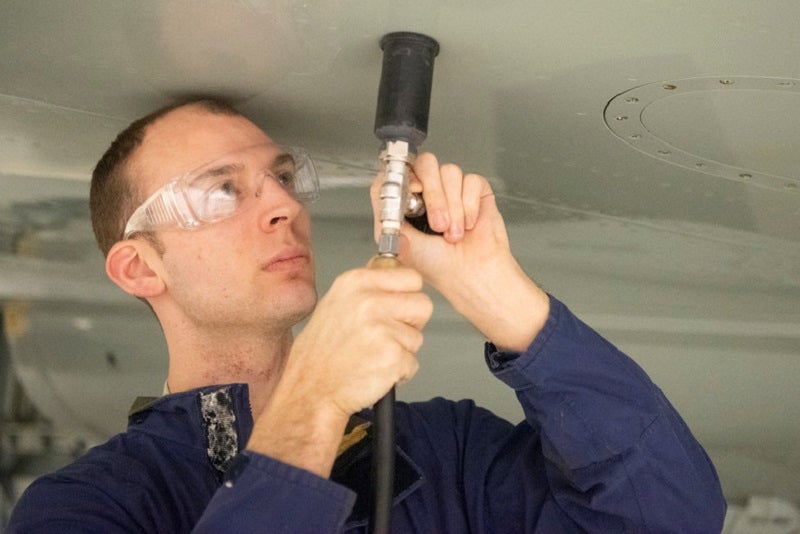
Royal Air Force (RAF) Mildenhall in the UK has unveiled a new device called the Pressurized Leak Detection Cup that can minimise the time needed to detect leaks within aircraft fuel tanks.
The Pressurized Leak Detection Cup was created by 100th MXS aircraft fuels systems craftsman Patrick Leach with the help of the aircraft structural maintenance flight.
Manufactured using 3D printers, the new detection cup is being used on the Boeing KC-135 Stratotanker, a military aerial refuelling aircraft for the US Air Force (USAF).
Leach said: “My innovation is a 3D printed cup which we can pressurise when pressed up against the surface of the aircraft. This allows air to travel through any open channels on the surface and exit on the inside of the tank. We can then apply soapy water to the inside so we can see where the leak is coming through.
“We’re also working on pushing it out for other aircraft and getting the technical orders changed to actually implement it airforce-wide.”
Using the cup, the time needed to detect leaks can be reduced by 75%. It improves the wing’s ability to quickly deliver mission-ready aircraft that can provide aerial refuelling.
How well do you really know your competitors?
Access the most comprehensive Company Profiles on the market, powered by GlobalData. Save hours of research. Gain competitive edge.
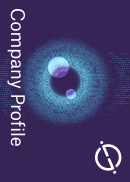
Thank you!
Your download email will arrive shortly
Not ready to buy yet? Download a free sample
We are confident about the unique quality of our Company Profiles. However, we want you to make the most beneficial decision for your business, so we offer a free sample that you can download by submitting the below form
By GlobalDataAdditionally, the detection cup minimises downtime for leak repair and allows maintenance personnel to accomplish other tasks.
100th MXS self-assessment programme and continuous process improvement manager Mia Tobitt said: “It costs under $15 in materials to produce and will save approximately $1.5m per year at RAF Mildenhall.
“Being 3D printed allows us the option to produce different forms of the cup so that it can be used for multiple applications.”