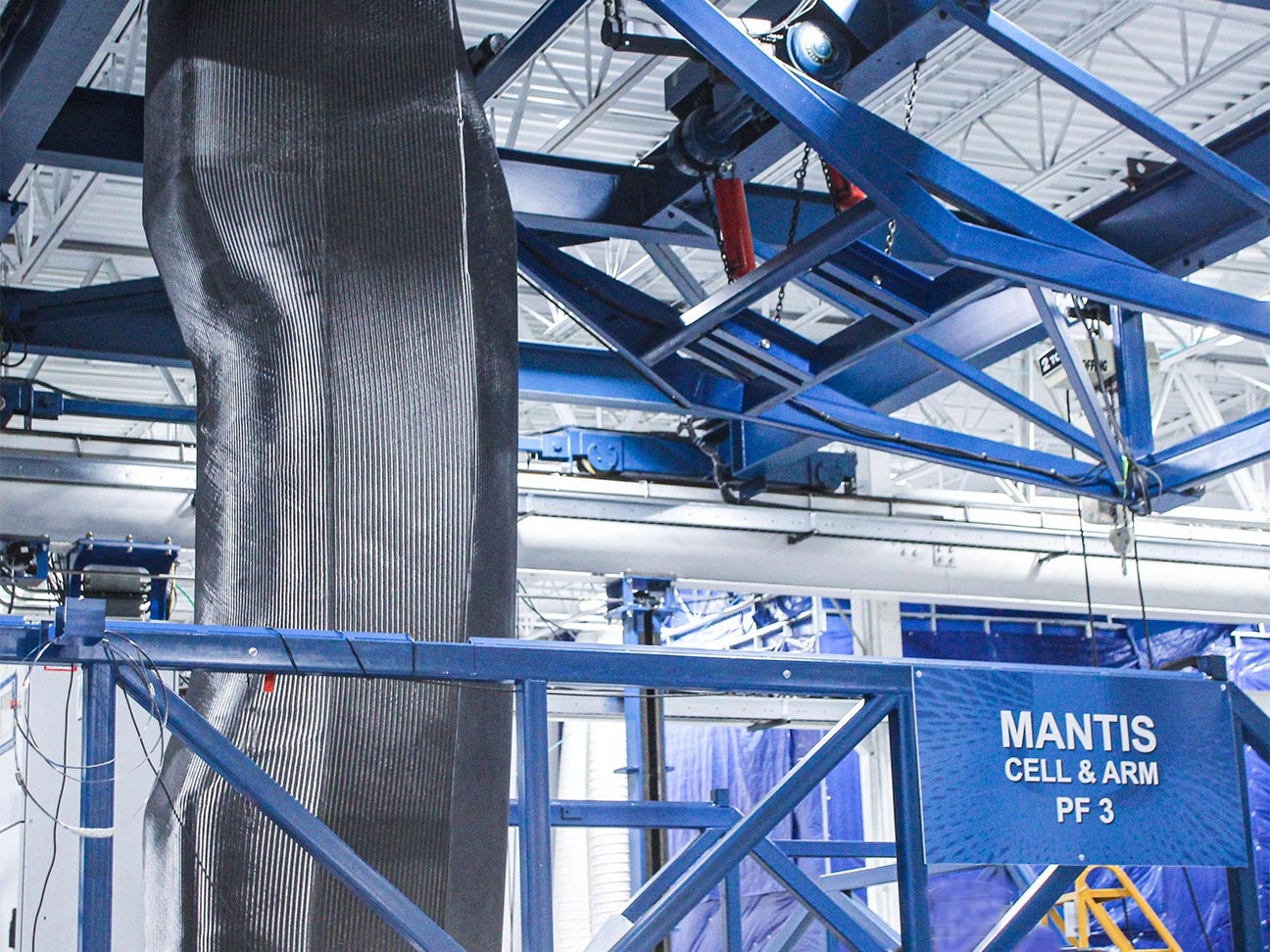
The US Air Force Research Laboratory (AFRL) has announced that its Aerospace Systems Directorate researchers and engineers team tested an attritable aircraft fuselage and wings design built at low cost.
The test was conducted on 14 September at Wright-Patterson Air Force Base (AFB) in Ohio, US, and forms part of the Design for Manufacture of Attritable Aircraft Primary Structure (DMAAPS) programme.
Attritable refers to a new class of uncrewed aircraft.
AFRL noted that enhancing the attritable aircraft technology is key to equipping troops with a tool that is easy to manufacture at a low cost, especially when there are tight time constraints.
The University of Dayton Research Institute (UDRI), Kratos, A&P Technology and Hawthorn Composites created a manufacturing solution for the primary structure of the attritable aircraft.
This new approach of the team helped in replacing more costly composite practices.
How well do you really know your competitors?
Access the most comprehensive Company Profiles on the market, powered by GlobalData. Save hours of research. Gain competitive edge.
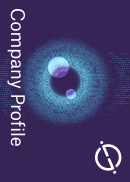
Thank you!
Your download email will arrive shortly
Not ready to buy yet? Download a free sample
We are confident about the unique quality of our Company Profiles. However, we want you to make the most beneficial decision for your business, so we offer a free sample that you can download by submitting the below form
By GlobalDataUS Air Force (USAF) considered this approach as an ‘effective technique’ in manufacturing aircraft fuselage and wing airframe structures in order to achieve swift production of airframe systems.
Aerospace Systems Directorate DMAAPS programme manager Ray Fisher said: “DMAAPS was conceived to evaluate the ability of an affordable design-for-manufacture approach to meet the form, fit, and function of a high subsonic unmanned military aircraft.
“Under DMAAPS, AFRL established a collaborative environment where an aircraft manufacturer worked with innovative Materials and Manufacturing Processes (M&P) owners to demonstrate and test an affordable and agile M&P approach.”
According to AFRL, the latest test is aimed at comparing the stiffness of the structure and strength of the wings and fuselage built using new manufacturing processes against the conventional aerospace M&P approach.
Aerospace Systems Directorate project engineer Matthew Durham said: “Each test has unique requirements and it can take many months for test systems design, manufacture of custom hardware to implement test parameters, configuration of the test article with instrumentation and test hardware, and overall systems integration.
“This DMAAPS preparation took only six weeks, since it was designed to leverage an existing test system, so our efforts were article configuration and test systems integration.”