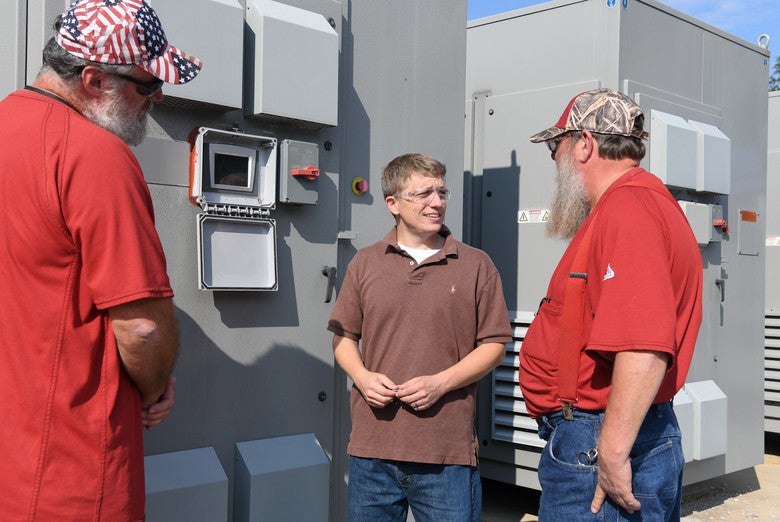
A team at Arnold Air Force Base (AFB) has made software modifications to detect unsafe conditions, avoid unnecessary downtime and prevent damages.
The Aerodynamics and Propulsion Test Unit (APTU), a blowdown wind tunnel designed for aerodynamic testing of supersonic and hypersonic systems and hardware at true flight conditions, recently experienced problems with a certain electrical component.
The software modifications addressed an uncommanded runaway of a rectifier, an electrical device that transforms alternating current into direct current.
Electrical engineer Adam Webb said: “A runaway is when the output current increases significantly above the set point value.”
The software modifications avoided unplanned test termination, fuel system damage and unscheduled test repeats.
Webb said: “A repeat test at APTU can be expensive and could cause additional degradation to the test article.”
How well do you really know your competitors?
Access the most comprehensive Company Profiles on the market, powered by GlobalData. Save hours of research. Gain competitive edge.
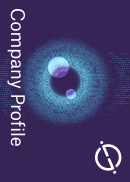
Thank you!
Your download email will arrive shortly
Not ready to buy yet? Download a free sample
We are confident about the unique quality of our Company Profiles. However, we want you to make the most beneficial decision for your business, so we offer a free sample that you can download by submitting the below form
By GlobalDataWebb enhanced the logic used in the programmable logic controllers on the units to handle uncommanded runaways, which enabled him to detect the part at fault.
Instrumentation data and controls engineer Gareth Penfold used a spreadsheet-based method to track equipment that needs calibration.
APTU group manager for test operations and sustainment at Arnold AFB Sharon Rigney said: “Gareth leveraged a previous spreadsheet method of tracking instruments into a fully functional computer database format.”
The database format includes an inventory of spare instruments available substitutions of failed items or items that require calibration.
The new database will also track warranty dates and time-sensitive data needed for engineering decision-making.
The APTU facility, which is capable of producing test conditions from Mach 3.1 to Mach 7.2, can support a myriad of test setups: propulsion, material, structures, store separation, and directed energy lethality / survivability.