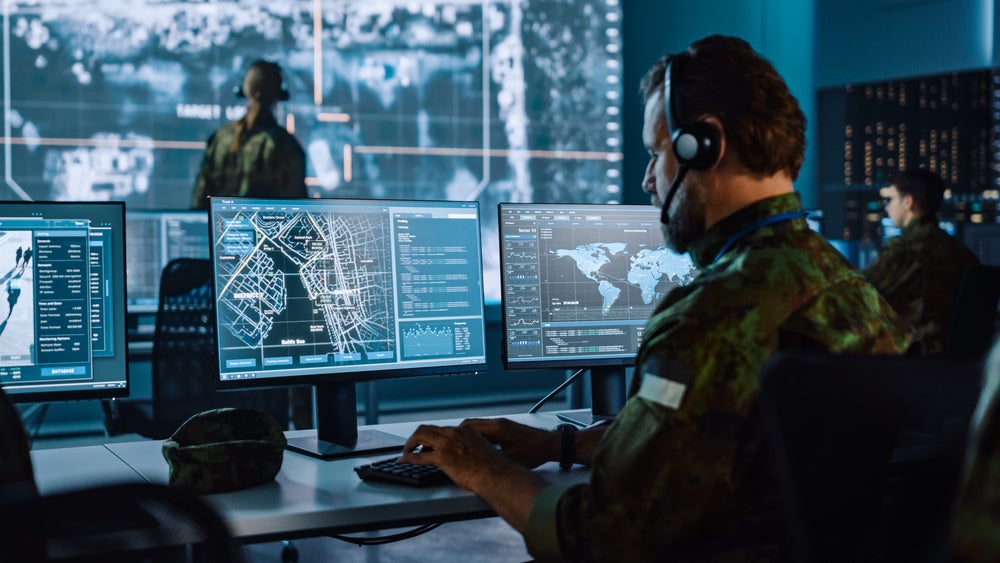
Digital transformation has changed the game for any industry. From industrial processes to medical sectors, military and defense, and space exploration, Industry 4.0 has introduced innovative technology that has transformed the electronic connector market.
There is a myriad of factors that contribute to changes in the global connector and cable market. Whether its new technologies such as automation and the Internet of Things (IoT), or issues related to the Covid-19 pandemic and international trade tensions, the shifts are continuous and staying ahead of the competition requires anticipating future trends. In collaboration with micro and nano-miniature connector experts Omnetics, we’ve identified five key trends that are driving innovation.
1. Using secure sensor, detector and surveillance systems to collect data
We are living in a digital era, and Internet of Things (IoT) networks are used for everything from industrial sensor systems to military surveillance. Not only does this require rugged, high-quality sensors to collect information, when dealing with mass data this needs to be processed using artificial intelligence (AI), machine learning (ML), and advanced analytics tools.
The importance of cyber and electromagnetic interference (EMI) security within these systems cannot be overstated. With the new capabilities that digital transformation has brought us, it has brought with it new challenges, and security is often at the top of the list. Cyber-attacks and intentional EMI in electronic warfare must be prevented with effective shields.
2. High-performance gigabit processing speeds at low voltages
With the internet revolution came a massive increase in data traffic. Typically, processors with high enough clock speeds (mhz) to handle mass data required higher voltages. Chips that offer gigabit processing speeds at low voltages not only enable mass amounts of data to be handled (without overclocking), but lower voltages require less power and produce less heat to allow components to operate optimally for longer. Low voltage electronics are also in demand from industries that deal with extreme environmental exposure.
3. Low Dk materials for higher-frequency PCBs
We’ve come a long way since dial-up internet access, and the shift towards wireless networks for applications such as satellite communication (especially with 5G becoming more widespread) has seen a growing trend in the development of high-frequency electronic devices.
Typically, FR4 laminates are used for printed circuit boards (PCB), but these can have poor dielectric constant (Dk) stability. The dielectric constant refers to the ratio of the electric permeability of a material compared to the electric permeability of free space (or vacuum permittivity). Having a low Dk prevents delay in signal transmission.
4. Digitisation of signal data using MBSE
According to the International Council on Systems Engineering (INCOSE): “Model-based systems engineering (MBSE) is the formalised application of modelling to support system requirements, design, analysis, verification and validation activities beginning in the conceptual design phase and continuing throughout development and later life cycle phases.”
In industry 4.0, digitalisation is essential, as traditional document-centric processes must give way to digital model-based processes and IoT technology. The sheer amount of data from numerous pipelines that digital transformation enables means that dealing with this data can be extremely complex, and monolithic systems can drastically reduce flexibility. MBSE can help to develop and verify digital process models in order to minimise risk by analysing process architecture and model approaches.
5. Mobility in the military and defense sectors
Defense and military industries are increasingly demanding high portability. This requires connectivity for autonomous robots, as well as dismounted soldiers, rescue, and recreational equipment. This is no easy task for an industry that can face extreme pressure and adverse environments.
To achieve effective mobile troop technology, there is a demand for miniature electronic sensors, detectors, transmitters and rugged wiring that is specifically designed to work on the active battlefield during high shock, vibration, and extreme environmental exposure.
How do these market trends impact connectors and cable?
There are a number of ways in which the design, development and manufacturing of connectors and cables are being adjusted to meet the requirements of emerging market trends.
Firstly, connectors need to be small, low-weight and rugged, and for interconnected systems there is a demand for the inclusion of multiple mates and de-mates. Additionally, there is a demand for multiple sets of differential signal sets that are shielded from others. Differential signal sets are ideal for low-voltage electronics and also have the advantage of resisting EMI.
When it comes to materials, new connector insulators and shells are being built with lower capacitance, low Dk materials, rather than FR4 weave. Additionally, cables used for PCBs are much shorter, if they are even used at all.
Current connector market trends demand very high pin counts to offer phased array data management (so it can be collected, stored, and accessed securely and efficiently), as well as better control of new laser-based transmission compared to older microwave broadcast.
For more than 30 years, Omnetics has been designing and manufacturing micro-miniature and nano-miniature electronic connectors and interconnection systems. Their extensive range of products are built with the future in mind, so customers can rest assured that they are ready for emergency market trends in Industry 4.0.
For more information about Omnetics’ offering, download the whitepaper below.