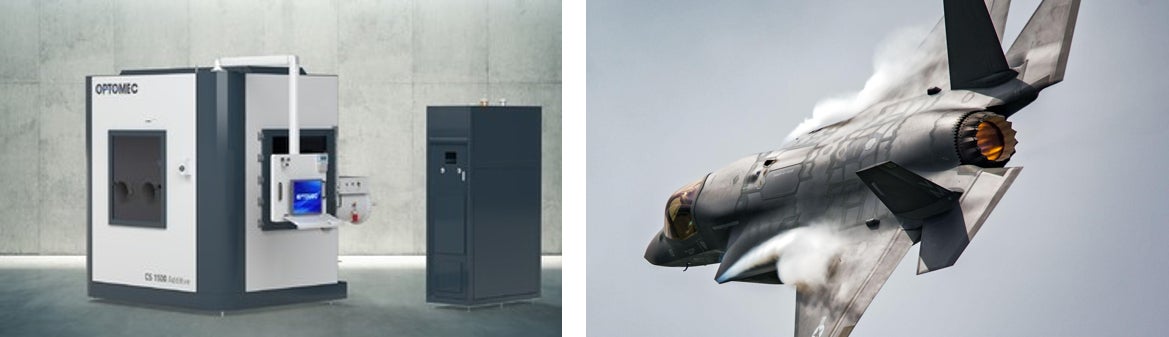
The US Air Force (USAF) has awarded a contract to Optomec to develop an additive repair process for the aircraft engines’ oversized titanium components.
The components are used on USAF aircraft, including the F22 Raptor and F35 Lightning II.
Under the $1.5m contract, Optomec will develop metal additive manufacturing system, which will help repair the parts.
The integrally bladed rotors (IBR), also known as the blisks, are single-piece compressor rotors that often gets damaged or worn out in the normal use.
Cost of replacing each of the lightweight, titanium-alloy blisks can amount to more than $500,000, noted the company.
With Optomec’s additive repair process, the USAF is expected to save more than 80% of the total repair cost, including tens of millions of dollars in annual investment.
How well do you really know your competitors?
Access the most comprehensive Company Profiles on the market, powered by GlobalData. Save hours of research. Gain competitive edge.
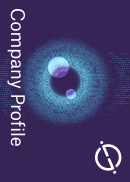
Thank you!
Your download email will arrive shortly
Not ready to buy yet? Download a free sample
We are confident about the unique quality of our Company Profiles. However, we want you to make the most beneficial decision for your business, so we offer a free sample that you can download by submitting the below form
By GlobalDataThe contract will see Optomec deliver and induct a five-axis LENS/DED metal printer, along with a work envelope of 5ft x 5ft x 3ft, which can handle blisks with diameter of up to 46in.
In addition, the system includes a proprietary gas purification system, which is required when depositing titanium to ensure superior metallurgical properties.
The gas purification system can maintain a moisture-free environment (<10ppm).
The company will examine different process monitoring techniques’ efficacy. The techniques are used to track main variables, which serve as measure for quality assurance and verification.
The project will also showcase feasible repairs for large blisks, as well as the restoration of foreign object damage (FOD) and representative wear across several areas of individual blades.
Optomec will also repair different sections of an aircraft’s large scale blisk for spin fit testing, which will be the primary step for qualification.
Optomec business development vice-president Jamie Hanson said: “Optomec is best positioned to deliver production solutions to this growing need, based on its proprietary machine, software and process capabilities, combined with its existing position as the market leader delivering machines for production repair of individual turbine blades.”