Aerojet Rocketdyne has successfully tested its Llarge class 92in diameter second stage solid rocket motor in simulated altitude conditions at the Arnold Engineering and Development Complex (AEDC), located at Arnold Air Force Base (AFB) in Tennesse, US.
The motor has been designed, fabricated and tested for the US Air Force Nuclear Weapons Center (NWC) at Hill AFB, Utah, under a demonstration contract that required use of available technologies applicable to multiple future common strategic propulsion systems.
The test was developed and executed in conjunction with AEDC’s operating contractor, Aerospace Testing Alliance.
Aerojet Rocketdyne Rocket Shop defence advanced programmes vice-president Tyler Evans said the stage is a significant improvement over currently fielded systems.
Evans said, "The application of this advanced design, using affordable materials and subsystems provided by our strong industrial base partnerships, will reduce future acquisition program costs and improve system reliability.
"These technologies are relevant across all air force and navy missiles, whether for strategic deterrence, prompt strike or other applications, and they are key to sustaining the needs of the nation’s warfighters."
How well do you really know your competitors?
Access the most comprehensive Company Profiles on the market, powered by GlobalData. Save hours of research. Gain competitive edge.
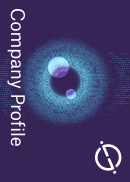
Thank you!
Your download email will arrive shortly
Not ready to buy yet? Download a free sample
We are confident about the unique quality of our Company Profiles. However, we want you to make the most beneficial decision for your business, so we offer a free sample that you can download by submitting the below form
By GlobalDataCreated by Rocket Shop staff, the stage has been integrated with affordability features, including the use of low-cost propellant common to the solid rocket boosters already in production, and a domestically sourced nozzle exit cone material, and is capable of being fielded for 35 years.
The General Dynamics facility has designed and fabricated the motor case at its facility in Nebraska, US, using domestically sourced carbon fibre, while the thrust vector actuation system was fabricated by Honeywell Aerospace in Tempe, Arizona, US.
Aerojet then cast the motor and assembled the stage at its facility in Sacramento, California, using facilities optimised for affordable production.
The company also utilised the contract to maintain and augment the solid rocket motor industrial base, which is a critical national need recognised by the Office of the Secretary of Defense (OSD).