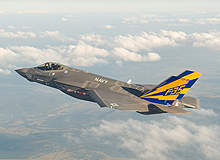
In a period of economic belt-tightening and military budget cuts, the F-35 joint strike fighter (JSF) development programme sticks out like a sore thumb. With total cost projections reaching $388bn and rising, this international development project has set a whole new scale for defence projects.
The F-35 Lightning II family of fifth-generation, multirole, stealth-capable fighter jets is set to be introduced into the US Air Force, as well as those of around ten other participating nations, in 2018. Main versions of the fighter include the F-35A conventional take-off and landing (CTOL) variant, the F-35B short take-off and vertical landing (STOVL) variant and the F-35C variant, which is customised for operation from aircraft carriers.
Development of the F-35 is being led by US aerospace and defence company Lockheed Martin, the X-35 prototype of which won the JSF competition over Boeing’s X-32 design in 2001. But the programme is truly global in scope, with other participating nations, especially the UK as a Level 1 partner, having input on design and development. In many respects, the JSF programme is the most complex military project ever undertaken.
As such, the immense challenge of testing the flight capabilities of the fighter and its variants, as well as the myriad electrical and mechanical components included in their design has been magnified by the project’s global scope. The F-35 must not only be rigorously tested to ensure it lives up to expectations; it must be tailored for the various needs of its future international users.
For example, the F-35I is a variant of the aircraft for use by Israel (a security cooperative participant in the programme), with the capacity to incorporate Israeli weaponry and electronic systems. The CF-35, meanwhile, is another variant of the fighter made for use by the air forces of Canada and Norway, which will add a drag chute for improved landing on icy runways.
Controlling costs
As should be expected at a time when costs are being intensely scrutinised, there is an immense amount of pressure on Lockheed Martin and other JSF contractors to develop and test the F-35 family on budget and within a strict time schedule. Throughout last year and continuing into early 2011, a host of reports from US authorities point towards trouble in the testing of the new jets, both in cost and punctuality. In March 2010, the US Pentagon announced that the JSF programme’s cost had risen by an extra 50% compared to projection at the project’s outset. The development programme is also reported to be several years behind schedule.
How well do you really know your competitors?
Access the most comprehensive Company Profiles on the market, powered by GlobalData. Save hours of research. Gain competitive edge.
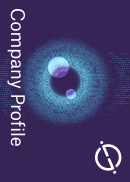
Thank you!
Your download email will arrive shortly
Not ready to buy yet? Download a free sample
We are confident about the unique quality of our Company Profiles. However, we want you to make the most beneficial decision for your business, so we offer a free sample that you can download by submitting the below form
By GlobalDataMany of these costly delays have stemmed from problems with the F-35B STOVL variant, conceived for use by the US Marine Corps and valued for its ability to land vertically. During test flights, problems ranging from the F-35B’s ability to achieve vertical landing with the projected fuel and weapon load to parts reliability and issues with auxiliary air inlet doors.
Partly as a result of these issues, the British Royal Navy, which had originally intended to procure a fleet of F-35Bs to replace its Harrier GR9s, has decided to order F-35C variant fighters for use on its new aircraft carriers instead. Even the marine corps, for which the F-35B was originally intended, has reduced its order for the STOVL aircraft. These problems place the development of the F-35B in serious jeopardy as reduced orders will drive costs up further.
In January 2011, US Secretary of Defense Robert Gates placed the variant on a two-year development ‘probation’, pending a redesign to resolve these problems. “If we cannot fix this variant during this time frame and get it back on track in terms of performance, cost and schedule, then I believe it should be cancelled,” said Gates.
Flight testing
Despite the ongoing issues with the programme, Lockheed Martin and its collaborators have reached many significant milestones in the testing of the F-35. Test flights under the programme are increasing, with pilots getting more time in the air to trial the advanced systems of the aircraft variants. According to Lockheed, 410 test flights were completed last year and 150 flights have already been logged as of March 2011.
Since the beginning of 2011, Lockheed has reported some promising test accomplishments. On 6 January, F-35 test pilot David Nelson captured the aircraft’s first maps using synthetic aperture radar, a computer-assisted radar capability that produces high-resolution images of the ground and is central to the F-35’s navigation systems.
Just over a month later, US Navy pilot Eric Buus became the first active-duty naval aviator to test the F-35C carrier variant.
“The in-air handling qualities of the F-35C are excellent. They are also very similar to the B variant. I immediately felt right at home in the aircraft,” he remarked. “The navy should be excited about having an aircraft that will be able to launch from our carriers with enough internal fuel and weapons to project power where we need to while having the stealth characteristics to go in and out of harm’s way unseen.”
Perfecting JSF’s components
While in-air test exercises may be the most high-profile and visible aspect of the F-35’s development, thousands of other technology and aerodynamics experts around the world are working behind the scenes to gather data essential to refining the aircraft’s design. At the US Air Force’s Arnold Engineering Development Center (AEDC) in Tennessee, more than 10,000 hours of testing has been undertaken in wind tunnel tests to analyse the aerodynamic properties of the F-35’s airframe and the performance of the engine. “We’ve tested all three versions in the wind tunnels,” said AEDC’s F-35 project manager Marc Skelley at the end of 2008. “There’s not a lot of difference aerodynamically between the CTOL and STOVL versions. The carrier version has much larger wings for creating more lift necessary to land on a carrier deck.”
Outside the US, contractors around the world are making contributions to the project. Chief among these is UK contractor BAE Systems, which is Lockheed’s prime sub-contractor on the F-35 project and has been responsible for many different elements of the development programme. It was BAE test pilot Graham ‘GT’ Tomlinson who piloted the first ever vertical landing of the STOVL variant in March 2010. “Today’s vertical landing onto a 95ft square pad showed that the aircraft has the thrust and the control to manoeuvre accurately both in free air and in descent,” said Tomlinson upon achieving the feat.
Most recently, a BAE-led UK industry team completed successful 600mph tests on the emergency ejection system that will be installed in all of the more than 3,000 F-35s that are expected to take to the skies under various air forces.
The tests, conducted at a Chalgrove Airfield facility in Oxfordshire, have refined the ejection system over several years, which is now ready to be implemented in the final production versions of the aircraft. “Ejecting from an aircraft like F-35 typically takes no more than three seconds from the time the ejection handle is pulled to the pilot being on a parachute,” said BAE test manager Rick Whittaker. “You can imagine how quickly everything happens. Incredibly, during the tests up to 900,000 measurements were recorded every second and I am pleased to say the systems performed really well.”
Signs this year seem to indicate that although cost estimates for the F-35 project have been blown out of the water and analysts are starting to describe it as a white elephant, steady progress is finally starting to be made. Although several years of development remain before the first production versions start rolling out, the complexity of systems that goes along with creating the world’s most advanced multirole fighter necessitates a long period of highly detailed analysis and refinement. Delays and cost increases are a somewhat inevitable consequence of testing a family of aircraft that is attempting to be all things to all people.