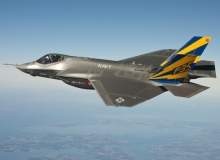
As various versions of Lockheed Martin‘s fifth generation fighter, the F-35, approach advanced stages of flight testing, the aircraft is undergoing close scrutiny from curious onlookers.
F-35 Lightning II
The F-35 Lightning II joint strike fighter (JSF), is being developed by Lockheed Martin Aeronautics Company for the US Air Force, Navy and Marine Corps and the UK Royal Navy.
One particular area of interest is likely to be its custom built lift fan engine, developed by Pratt & Whitney using technology patented by Lockheed Martin and produced by Rolls-Royce.
A rival to the F135, the General Electric and Rolls-Royce-built F136 had been in development up until December 2011, but was dropped after the Pentagon refused to support further development.
Capable of catering for the demands of all three F-35 variations while ensuring an ease of maintenance and reduced downtime, the F135 has taken almost 30 years of development, but now looks ready to power the future fighter of the US and a host of European nations.
How well do you really know your competitors?
Access the most comprehensive Company Profiles on the market, powered by GlobalData. Save hours of research. Gain competitive edge.
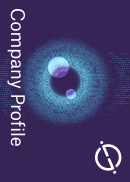
Thank you!
Your download email will arrive shortly
Not ready to buy yet? Download a free sample
We are confident about the unique quality of our Company Profiles. However, we want you to make the most beneficial decision for your business, so we offer a free sample that you can download by submitting the below form
By GlobalDataDevelopment and origins of the F135 engine
The first origins of the F135 lie in Lockheed Martin Skunk Works’ F100-229-plus demonstrator engine.
The first origins of the F135 lie in Lockheed Martin Skunk Works’ attempts to develop a stealthy short take-off and vertical landing (STOVL) fighter for the US, as part of DARPA’s ASTOVL programme in 1986. A concept aircraft and propulsion system was developed and patented by Lockheed’s chief aeronautical scientist Paul Bevilaqua.
Components from F119 and F100-229 engines were used to create the F100-229-plus demonstrator engine, which went onto prove Bevilaqua’s lift fan concept and ultimately lead to the development of the F135 for use on Lockheed Martin’s F-35.
The F135 team responsible for the development of the engine consists of Pratt & Whitney, Rolls-Royce and Hamilton Sundstrand. Through production techniques and materials, the F135 is available at cheaper prices than the F119, despite being a more powerful engine.
Two-shaft engine design of the F135 and variations
Both the conventional and carrier engines are largely similar and produce almost identical results, with a maximum wet thrust of 43,000lbf and a dry thrust of 28,000lbf.
The F135 is a two-shaft engine featuring a three-stage fan and six-stage high pressure compressor. The hot section comprises an annular combustor with a single-stage high pressure turbine unit and a two-stage low pressure turbine. The engine’s afterburner also features a variable converging-diverging nozzle.
Three engine variants have been designed; the F135-PW-100 and F135-PW-400 for use aboard the conventional and carrier versions of the aircraft respectively, and the F135-PW-600 for the STOVL variation. Both the conventional and carrier engines are largely similar and produce almost identical results, with a maximum wet thrust of 43,000lbf and a dry thrust of 28,000lbf. The major difference is the use of salt-corrosion resistant materials in the carrier variant.
The STOVL engine, however, is capable of producing different results courtesy of its design and the demands placed upon it.
Enabling short or vertical lift-off with the STOVL F-35 variant
The STOVL variation of the F-35, to be used by the US Marine Corps and UK Royal Navy, used Lockheed Martin’s patented Rolls-Royce LiftSystem, developed by Rolls-Royce.
Composed of a lift fan, drive shaft, two roll posts and a 3 Bearing Swivel Module (3BSM), the system is responsible for allowing the vertical lift-off required to operate aboard some aircraft carriers.
The 3BSM acts as a thrust vectoring nozzle, allowing the exhaust to be directed downwards to enable vertical lift-off. The lift fan, located towards the front of the aircraft, acts as a counterbalance by using two counter-rotating blisks.
Unheated engine bypass air is then diverted through nozzles mounted on the wings of the aircraft, called roll posts, in order to allow roll control.
The system is capable of handling 18,000lbf of dry thrust through the 3BSM, 20,000lbf through the lift fan and a further 3,900lbf through both roll posts, totalling 41,900lbs of thrust. The system, developed purposefully for the F-35 programme, received the Collier Trophy for achievements in aeronautics in 2001.
The 3BSM acts as a thrust vectoring nozzle, allowing the exhaust to be directed downwards to enable vertical lift-off.
Keeping F-35s in the air: reliability and maintenance
One major directive of the development of the F135 engine was to drastically improve engine reliability and ease of maintenance over previous aircraft, keeping downtime at a minimum. One such method was to use far fewer parts in comparison to similar engines, theoretically reducing parts failures, and ensuring that all line-replaceable components can be changed using a standard set of six common tools.
The major leap forward has, however, been the establishment of the F135 Health Management System, which monitors the performance of the engine automatically and provides real-time data to maintainers on the ground. This data is analysed before maintainers troubleshoot and identify any necessary replacement parts prior to the aircraft returning to base. Pratt & Whitney has estimated that this could save as much as 94% of replacement time over legacy engines, achieving the directive of reducing aircraft downtime.
Fifth generation fighter competition: Russia and China enter the fray
Although the F135 has been developed for the F-35, with other fifth generation fighters currently in development, it will inevitably be judged against its rival engines.
The Sukhoi PAK FA, developed for use by the Russian Air Force and Navy, uses a custom built engine, the 117. Although the finer details of the engine are shrouded in predictable secrecy, Sukhoi general director Mikhail Pogosyan confirmed that in comparison to the AL-31 engine, 117 is 150kg lighter and provides 2.5 tons more thrust, enabling the PAK FA to supercruise.
It has further been alleged that the engine possesses a complex automation system to enable various fight modes, with each engine widely expected to be capable of independently vectoring its thrust upwards, downwards and to either side. This would allow the engine to produce a twisting force, making the PAK FA the first fifth generation fighter with full 3D thrust vectoring across pitch, yaw and roll axes, something which could see it propose an entirely new challenge.
More competition will come from China’s Chengdu J-20, although the aircraft is some way behind its rivals and, subsequently, detailed information regarding engine performance is sparse. Although it was initially reported that Russia’s 117 engines could be provided for the aircraft, it has also been reported that China has chosen to indigenously develop high thrust turbofan engines, fitted with thrust vector controlled nozzles to power the aircraft.